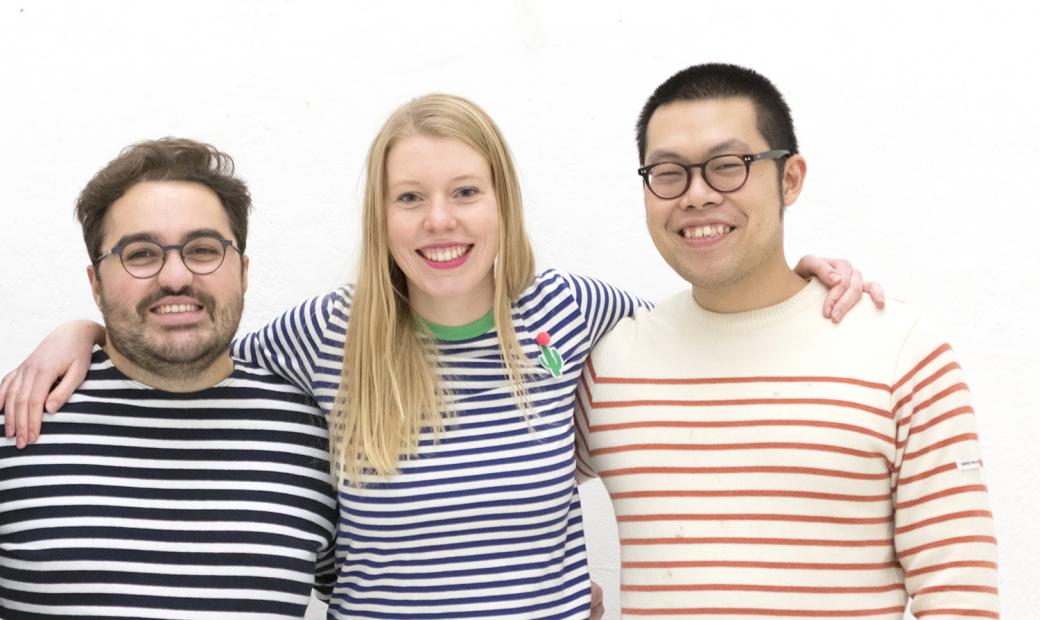
Hi re:flex! Could you briefly describe who you are and where you are from?
Hey! We are Benton Ching, Pierre Azalbert and Karlijn Sibbel, a multidisciplinary team of designers, engineers and science-enthusiasts. We met each other while studying Innovation Design Engineering at the Royal College of Art and Imperial College in London. Benton moved to London from Australia where he studied Political Philosophy before. Pierre, on the other hand, is originally French but studied Electrical Engineering in London before doing his masters. And lastly, Karlijn studied Product Design at ArtEZ in the Netherlands after growing up in Wageningen, not far from there.
What best describes you as designers?
We like to think we’re somewhere between explorers, tinkerers and experimenters. Our work stems from combining research and experimentation from the academic backgrounds we have.
Where do you look for inspiration?
We are inspired by systems and processes in nature, and by insights that come about from making connections between seemingly disparate fields of research. We enjoy reaching out to specialists to discover their specific field and research interests: it can be really inspiring and rewarding to dive into new fields of science as an outsider as it can often bring about connections that might sit outside the boundaries of a particular discipline.
You're a multidisciplinary team with a passion for bridging the gap between scientific research and everyday life. What does an average day in your studio look like?
Haha, never the same! The thing we enjoy doing the most is working in the workshop/lab to make new tests and prototypes. But equally some days are filled just with meetings to explore collaborations with industry or researchers, or diving into scientific papers to do research. As a team, we try to shift the roles we take on, which makes it more fun to work together and learn new things. At the moment we are doing a residency at Makerversity, which gives us a lot of opportunities to conduct experiments as well as meet other designers and makers.
You mention your work re:flex is inspired by nature. Are you familiar with the concept of biomimicry? If so, how do you think this applies to your designs?
When developing our material, a paper that really inspired us was a paper by the physiologist J.Scott Turner and the architect Alan Penn which talked about adaptation and biomimicry. An interesting distinction that started to emerge was between biomimicry and nature-inspired engineering, albeit one with slightly fuzzy boundaries.
Pierre came up with a really interesting working definition, which is that biomimicry looks at how nature has adapted to change, while nature-inspired engineering looks for more higher-level principles of how nature is adapting. That is to say, the former looks at emulating morphological changes in organisms arising from their development in specific contexts, while the latter looks at the principles behind these developments.
Although there are really interesting insights to be gained from both approaches, we took a nature-inspired engineering approach when doing initial research for re:flex.
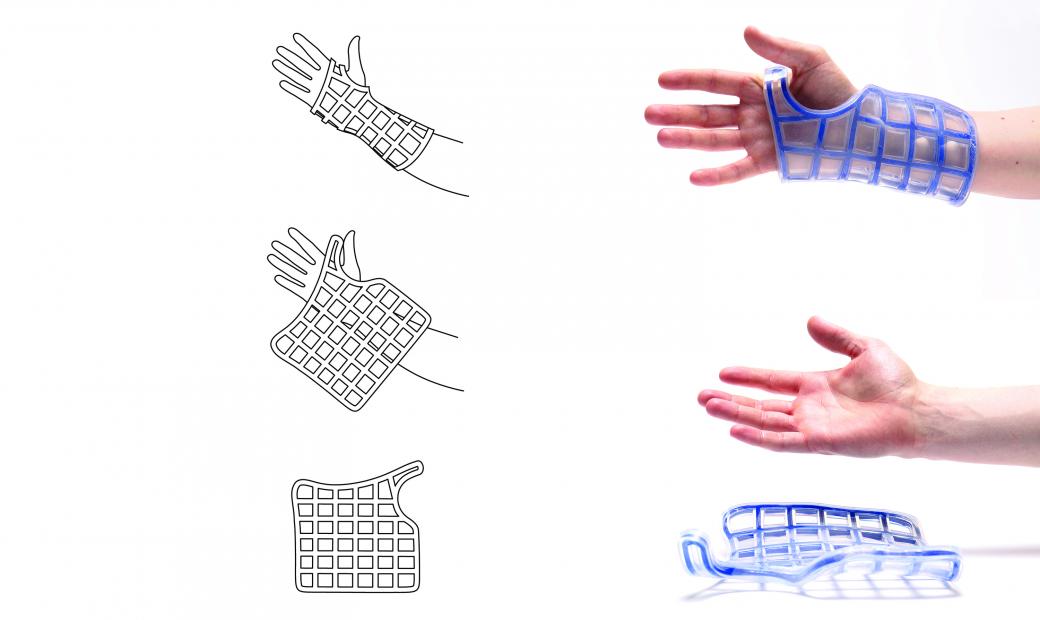
You imagine a world where materials are no longer inert, allowing objects to adapt to the needs of the user. How would such a world look? And how would we live in it?
This idea of an active world is really inspired by nature - based on its ability to constantly adapt and reconfigure. It would be a world where smart materials allow objects to be transformed or transform by themselves. The interesting ability that shape-changing materials give us is that they can change their purpose and use by transforming into a different shape. This would translate for instance in an object that forms around different bodies or products that can have multiple uses or even owners.
If you would zoom out to a system-level rather than individual level, these smart materials would ideally respond to changes in their direct environment and therefore adapt our surroundings according to what is needed. Think about passive cooling systems, for instance, creating shade and direct the wind through a city. Or imagine a city responding to pollution levels or changes in weather. It is the vision of a ‘living’ and ‘breathing’ world that has captured the imagination of people for decades.
Termites are a concrete example from nature in this for instance. The workers constantly adapt and reconfigure the tunnels in their mound to regulate the flow of heat, oxygen, and moisture in response to changing conditions outside of their nest. It is this ability of the termites that make them so resilient to change.
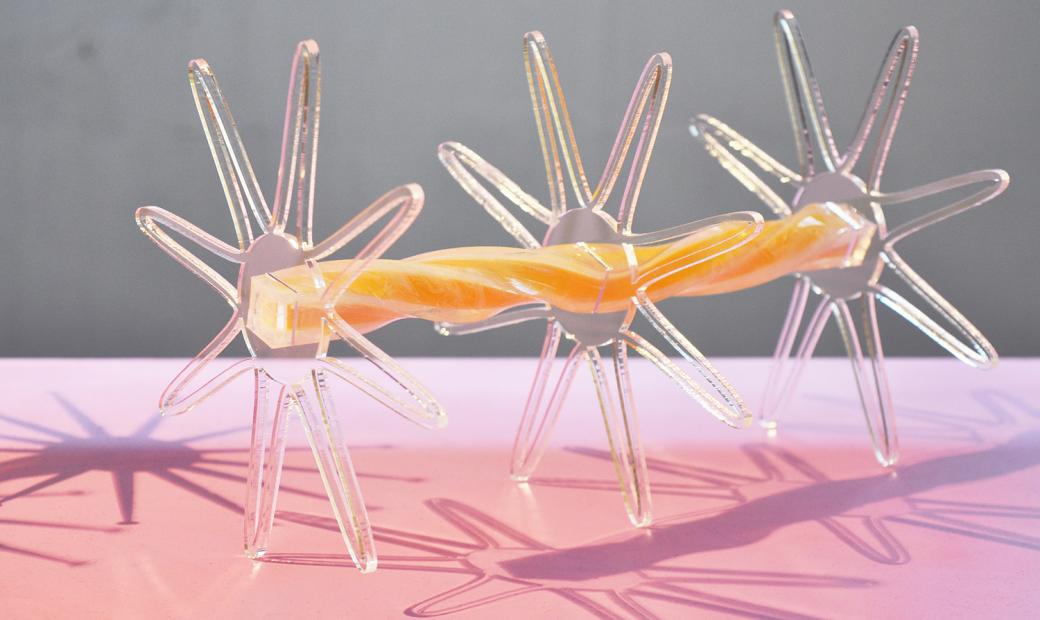
What would you ultimately like to achieve with re:flex?
The ultimate goal we would like to achieve with re: flex would be to promote behaviour change around material usage. At the moment there seems to be a mismatch between the kinds of materials we use and the purposes they are intended for. For example, we use materials that last for hundreds of years in products that are used for a few days and sometimes even for seconds. Additionally, we often fail to see how materials are part of a larger system and how we should deal with them accordingly. These are problems that we are becoming more aware of and require a behaviour change around material usage. An interesting quote from Philip Ross from Mycoworks that explains this well is: “There is not so much a crisis of materials, but of how we think about them, organise them and use them.”
We hope to contribute to discourse around this issue by exploring how products can have a longer life-time by making them adaptable. We do this by exploring the possibilities of using smart materials that can move and change shape easily in response to heat. Although these materials have been around for decades we don’t use them in our daily life. As these materials give completely new and sometimes complicated possibilities, we want to explore and share these possibilities by showing; t heir unique aesthetic and functional properties in everyday contexts and by making them accessible to designers and makers.
You’ve experimented with temperature. What other natural elements would you like to experiment with for future designs?
It would be interesting to experiment with materials that react to moisture levels, UV-light or magnetic fields for instance. Which already exist! But we first want to focus on developing re:flex further and experiment with different material combinations that respond to different temperature ranges.
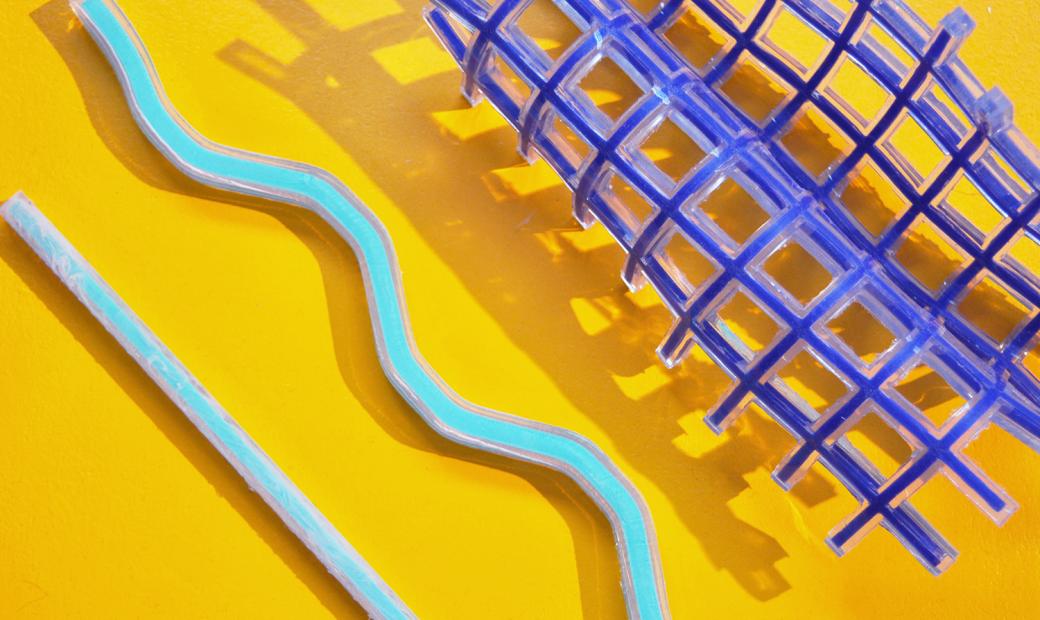
If you were able to choose anyone in the world to work with (a designer, politician, artist, scientist or someone else), who would that be and why?
I think that might be different for each member of the team! On one hand, there are so many material properties and applications we could explore with re:flex in a range of industries. We love to imagine how a big sportswear company might make reconfigurable or adaptable footwear of protective equipment with our material, or how a hospital might benefit from having quick custom fits made to orthotics or prosthetics. 

On the other hand, we’d love to conduct more fundamental research on shape changing materials. The Morphing Matter Lab at Carnegie Mellon would be really cool to work with. They have a lot of resources in terms of machinery, knowledge and talent in the field of Morphing Materials. It would be a dream to work with them!
Last Dutch Design Week (DDW) you exhibited re:flex at VEEM. What kind of response(s) did you get?
It was a great experience to be part of the exhibition in the VEEM gebouw because the public that comes there is so diverse! It was great to have conversations with people from different ages and see how they reacted to the samples and pieces we made.
People were really interested to learn how the material works and then what we can do with it. We also received some fun new ideas to embody re:flex in different ways. We also received a lot of questions regarding the environmental aspect of re:flex, which lead to more interesting conversations regarding sustainability and the need for behaviour change around materials.
Do you have any news you would like to share with the DDW community?
Yes! There are some exciting things coming up for re:flex. Especially now that we are working at Makerversity in London we have the ability to research and make many more things. Although we can’t share it yet we would definitely recommend staying tuned through our social media or by signing up to our newsletter!
Hey Designer! Do you also want to be featured on our website? Use #heyddw on Instagram, and who knows, you might be next!